Compressore assiale
turbomacchina operatrice a flusso assiale Da Wikipedia, l'enciclopedia libera
Il compressore assiale è una turbomacchina operatrice a flusso assiale per comprimere dei gas, nella quale il gas scorre parallelamente all'asse di rotazione.

Rispetto al compressore centrifugo gestisce maggiori portate a parità di superficie frontale, ma con un minore rapporto di compressione e quindi maggiori lunghezze per singolo stadio.[1] Nella turbina a gas, i compressori assiali sono collegati alla turbina da alberi di trasmissione rotanti. Quasi tutte le turbine a gas di taglia medio-grande di oggi sono a flusso assiale, mentre i motori più compatti, come le APU (unità ausiliarie di potenza) o i motori di elicottero o autoarticolato, sono a flusso centrifugo.
Descrizione
Riepilogo
Prospettiva

Un tipico compressore assiale possiede un rotore, un disco con palettatura, seguito da uno statore, e questo è fisso al telaio. L'accoppiamento di uno statore e di un rotore (l'ordine dipende dal motore) è detto stadio. Lo Junkers Jumo 004 (1943), uno dei primissimi turbogetti, possedeva otto stadi, il Lyulka AL-21F (primi anni 1960) ne possedeva ben 14, il General Electric J79 (fine anni 1950) addirittura 17. I moderni motori a getto invece, migliorando il rapporto di compressione di un singolo stadio grazie all'impiego di materiali più adatti e dall'aerodinamica più raffinata, possiedono un numero di stadi più limitato, sebbene utilizzino due (o più) compressori in serie, il compressore di bassa pressione ed il compressore di alta pressione mossi da alberi separati che ruotano a velocità differenti per ottimizzarne i rendimenti. Il Klimov RD-33 (anni 1970) usa 4 stadi per la ventola e 9 per il compressore, l'Eurojet EJ200 (anni novanta) invece 3 per la ventola ed appena 5 per il compressore.
Procedendo nel compressore, il volume di aria a disposizione del flusso si riduce mentre la pressione totale aumenta.
In un motore a getto il compressore è mosso da una turbina posta davanti allo scarico della camera di combustione. La turbina utilizza quindi una parte dell'energia liberata dalla combustione per muovere il compressore, tipicamente dal 60 al 65%, la frazione rimanente di energia viene impiegata nell'ugello di scarico per generare la spinta propulsiva.
Teoria
Riepilogo
Prospettiva

Il comportamento di un singolo stadio di un compressore assiale, nelle ipotesi semplificative di velocità radiale nulla e velocità assiale costante, è illustrato in figura, dove si trovano u1 la velocità assoluta di ingresso nel rotore, u2 la velocità assoluta di uscita dal rotore, w1 la velocità relativa di ingresso nel rotore, w2 la velocità relativa di uscita dal rotore e con U la velocità di rotazione del rotore. Inoltre si sono specificati con ut la velocità tangenziale assoluta di entrata e con pedice a la velocità assiale assoluta di entrata. Analogamente per w, la velocità relativa al rotore. Le velocità relative allo statore mostrano il pedice 2.
Osservando la figura si può notare (così come si può ricavare dall'analisi dei triangoli di velocità) che nel rotore le palette divergono, così che il flusso nel sistema di riferimento del rotore si comporta come in un condotto divergente (diffusore). Analogamente anche la palettatura dello statore è divergente per permettere la conversione di energia cinetica in energia meccanica di pressione.
Come nel compressore centrifugo, anche nel caso del compressore assiale si può ricavare che la potenza è proporzionale al quadrato della velocità di rotazione.
- Il singolo stadio di un compressore assiale può produrre solo un salto di pressione molto basso (1,15 - 1,30) senza rischiare instabilità o ridurre eccessivamente il rendimento (forti gradienti di pressione negativi nel flusso tra le pale, simile a quello in un diffusore).[1]
- Il compressore assiale si presta bene al pluristadio: il flusso in uscita dallo statore è già pronto per l'ingresso nello stadio successivo.
Le palette debbono essere svergolate, cioè presentare un diverso angolo rispetto alla corrente a seconda della distanza della sezione dal centro di rotazione. Infatti la velocità relativa tra corrente e paletta cambia a seconda di questa distanza (la velocità lineare di rotazione è infatti data dalla formula U = r × ω, dove U è la velocità lineare, r il raggio o meglio la distanza dal centro di rotazione ed ω la velocità angolare, o il numero di giri al secondo moltiplicato per la lunghezza di un giro, 2π).
Sviluppo
Riepilogo
Prospettiva



I primi compressori assiali offrivano una efficienza assai limitata, talmente limitata che nei primi anni '20 si pensava che in pratica un motore a getto fosse impossibile da costruire. Ma le cose cambiarono radicalmente quando Alan Arnold Griffith pubblicò un saggio nel 1926, nel quale si affermava che responsabili della scarsa efficienza del compressore erano le palette piatte usate all'epoca, le quali stallavano a qualsiasi numero di giri. Le prime palette infatti erano semplici "piastrelle", mentre lo studio di Griffith mostrava il vantaggio di palette a sezione alare, cioè spesse vicino al bordo d'attacco e appuntite sul bordo d'uscita. Il suo studio mostrava un diagramma dove una seconda turbina muoveva un'elica.
Sebbene Griffith fosse molto ben conosciuto per i suoi primi studi sulla fatica dei metalli e le misure degli sforzi, svolse ben poco lavoro direttamente connesso al saggio del 1926. L'unica conseguenza immediata fu un prototipo di compressore costruito da un collega di Griffith al RAE, Haine Constant. I primi tentativi di motore a getto, se si eccettuano quelli di Henri Coandă e di Giovanni Battista Caproni (si veda il motoreattore), vennero eseguiti da Frank Whittle e da Hans von Ohain utilizzando il più conosciuto compressore centrifugo, ampiamente impiegato per la sua robustezza, compressione, leggerezza e bassa inerzia, per i turbocompressori dei motori a pistoni.
Griffith valutò il lavoro di Whittle nel 1929, scartandolo come null'altro che un errore matematico ed affermò che una sezione frontale tanto grande sarebbe stata un ostacolo insormontabile per un aereo ad alte prestazioni.
Il vero lavoro sui compressori assiali iniziò negli anni '30. In Inghilterra Haine Constant raggiunse un accordo con una compagnia di turbine a vapore, la Metropolitan Vickers (od anche Metrovick), nel 1937, iniziando a dirigere i suoi sforzi verso il motore turboelica, basato sulle idee di Griffith, nel 1938. Nel 1940, dopo i successi del motore centrifugo di Whittle, Constant iniziò a lavorare sul getto puro, il Metrovick F.2.
In Germania Hans von Ohain aveva già prodotto diversi motori centrifughi, alcuni di questi avevano anche volato, ma tutti gli sviluppi furono poi indirizzati verso i Junkers ed i BMW a compressore assiale.
Negli Stati Uniti d'America sia Lockheed Corporation che General Electric vinsero commesse per la fornitura di motori a getto assiali, prima turbogetti e poi turboeliche. Anche la Northrop lavorò ad un proprio turboelica, che la Marina comprò nel 1943. Persino la Westinghouse entrò nella competizione nel 1942 con il J30.
Negli anni cinquanta praticamente tutti i motori più potenti erano dotati di un compressore assiale. Come Griffith aveva rilevato nel 1929, il più elevato ingombro assiale del compressore centrifugo era causa di una resistenza aerodinamica eccessiva rispetto al più stretto compressore assiale. Inoltre il compressore assiale poteva garantire eccellenti rapporti di compressione semplicemente aggiungendo degli stadi, creando un motore leggermente più lungo.
Per quanto riguarda il compressore centrifugo, questo è molto più semplice da disegnare, è più corto, più leggero e garantisce prestazioni inarrivabili per singolo stadio. Questo è il motivo per il quale è utilizzato su elicotteri ed APU, dove l'ingombro totale ed il peso giocano un ruolo più marginale.
Motori a getto a flusso assiale
Riepilogo
Prospettiva
Nelle applicazioni sui motori a getto, il compressore si trova ad affrontare una grande varietà di condizioni operative. A terra, durante il decollo, la pressione (statica) all'imbocco è elevata, mentre la velocità di imbocco è nulla ed il compressore attraversa una grande varietà di velocità quando viene azionato. Una volta in volo la pressione (statica) all'imbocco scende, ma la velocità, sempre all'imbocco, sale a causa del movimento dell'aeroplano, recuperando parte della pressione ed il compressore tende a girare a velocità di rotazione costante per lunghi periodi di tempo.
Semplicemente non esiste un compressore che si adatti a tutti questi stati di funzionamento. I compressori a geometria fissa, come quelli montati sui primi motori a getto, avevano un rapporto di compressione piuttosto limitato, circa 4 o 5 ad 1. Come per qualunque motore a combustione, il consumo specifico è fortemente in relazione con il rapporto di compressione, così vi fu una forte necessità economica nel migliorare gli stadi del compressore oltre questi rapporti di compressione.
Oltretutto il compressore poteva stallare se le condizioni all'imbocco cambiavano improvvisamente, un problema comune nei primi motori. In alcuni casi, se lo stallo avveniva vicino all'imbocco del motore, tutti gli stadi da quel punto in poi smettevano di comprimere l'aria. In questa situazione l'energia richiesta per far girare il compressore diminuiva rapidamente (dato che il compressore non compiva lavoro) e quindi l'aria calda rimanente a valle del combustore faceva girare ancora più velocemente la turbina e ciò che questa trascinava, ovvero il compressore stesso. Questa condizione, conosciuta come surging (o surge in inglese), fu uno dei problemi più importanti nei primi motori e poteva portare le giranti della turbina o del compressore a ruotare tanto velocemente da staccarsi dall'albero ed essere scagliate fuori dal motore.
Per queste ragioni i compressori assiali sono considerevolmente più complessi di quelli dei primi turbogetti.
Alberi
Praticamente tutti i motori moderni sono concepiti con due compressori, il primo a bassa pressione ed un secondo di alta pressione. Su motori di elevato diametro sono stati introdotti anche tre alberi concentrici per ottimizzare la velocità di rotazione delle varie sezioni del compressore in relazione alle dimensioni delle palette. Ogni compressore è mosso dal proprio albero, trascinato a sua volta da una turbina, rispettivamente di bassa o di alta pressione. Questo sistema consente di aumentare l'efficienza del motore.
Spillamento del flusso, statori a geometria variabile
Quando un aeromobile cambia velocità o quota, varia di conseguenza la pressione dell'aria all'imbocco del compressore. Per fare in modo che il compressore si adatti alle varie condizioni, sin dagli anni '50 si è cominciato a spillare (ovvero sottrarre) aria a metà del compressore; in questo modo il carico di lavoro del compressore diminuisce e si evita che negli ultimi stadi vi sia un volume eccessivo di aria. Questo accorgimento è sfruttato in particolar modo all'avviamento del motore, infatti è comprensibile che quando gli stadi rotorici inizino a ruotare non comprimano il flusso alla massima efficienza, cosicché negli stadi finali il volume d'aria sarebbe troppo grande se una parte non ne fosse spillata. La parte di aria spillata viene impiegata anche per raffreddare le palette della turbina, l'organo più sollecitato sia meccanicamente che termicamente. Le palette sono cave all'interno e le più sofisticate posseggono fori per la circolazione dell'aria. Infine l'aria del compressore viene usata sia per pressurizzare la cabina, per l'aria condizionata.
Un disegno più avanzato, a statore variabile, usa palettature che possono essere ruotate individualmente attorno al loro asse, in opposizione all'asse di potenza del motore. Per l'avviamento possono essere ruotate per "aprire", riducendo la compressione, per poi essere ruotate indietro verso il flusso a seconda delle condizioni esterne. Il General Electric J79 è il primo esempio di statore a geometria variabile, ed oggi è una caratteristica comune di molti motori militari.
Chiudendo progressivamente gli statori variabili, mentre la velocità del compressore diminuisce, si riduce la pendenza della curva di stallo (o di pompaggio) della macchina, migliorando il margine di lavoro della macchina. Incorporando statori variabili nei primi cinque stadi, la General Electric ha sviluppato un compressore assiale a dieci stadi in grado di operare ad un rapporto di compressione di 23:1.
Ventola
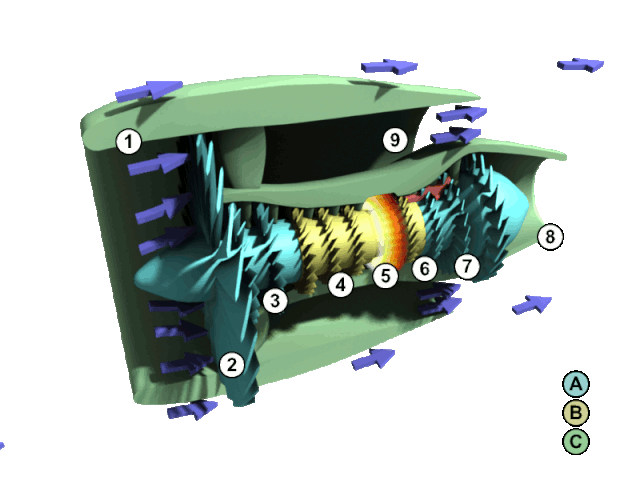
Nei motori a getto, la spinta è generata dalla variazione di quantità di moto dell'aria trattata. Una stessa spinta si può ottenere accelerando una grande massa di aria a basse velocità o una piccola massa di aria ad alte velocità. Alte velocità di efflusso comportano peggiori rendimenti propulsivi e problemi di rumorosità, ma sono a volte indispensabili per raggiungere elevate velocità di volo.
Al contrario, lo spostamento di una gran massa di aria a velocità relativamente bassa pone problemi di ingombro e di maggiore resistenza nelle fasi di volo in cui non è richiesta la massima spinta, dato l'aumento della sezione frontale del motore necessaria a trattare la maggiore quantità di aria.
Verso la fine della seconda guerra mondiale venne sperimentato in diversi progetti tedeschi (con il motore Daimler-Benz DB 670) e britannici (con il Metropolitan-Vickers F.3) l'utilizzo di una frazione della potenza disponibile alla turbina per azionare una ventola (o fan dagli inglesi) per un flusso di aria aggiuntivo che non veniva fatto passare per la camera di combustione.
La ventola è generalmente calettata sullo stesso albero che muove il compressore di bassa pressione, ma specialmente per motori di elevato diametro ad alto rapporto di bypass, può anche essere mossa da un albero a lei dedicato come nel Rolls-Royce Trent 1000 o da un riduttore di giri collegato all'albero di bassa pressione come sul Pratt & Whitney PW1000G. Su motori a basso rapporto di diluizione (in particolare destinati a velivoli militari da combattimento) è frequente l'impiego di ventole a due stadi in grado di aumentare il rapporto di compressione del fan e contenere gli ingombri trasversali.
Turboreattori a doppio flusso

Con il miglioramento dei rendimenti delle turbomacchine, si rese disponibile una potenza all'albero sempre maggiore. Nei primi anni cinquanta, la Rolls-Royce sviluppò il primo motore turboventola ad entrare in servizio, il Conway.
In questa tipologia di motori, l'aria in ingresso viene separata in un flusso caldo, destinato ad attraversare la ventola, il compressore, la camera di combustione e la turbina, ed un flusso freddo che è trattato solamente dal fan. Se i due flussi escono dal medesimo ugello di scarico, il motore viene detto a flussi associati, altrimenti a flussi separati.
Un turboventola a flussi associati, miscelando il flusso freddo con quello caldo proveniente dalla turbina, introduce anche il beneficio di abbassare la temperatura dei gas di scarico. In più, dal momento che il rumore di un turbogetto è proporzionale all'ottava potenza della velocità dei gas di scarico, il sistema di diluizione abbassa la velocità media dei gas di scarico riducendo sensibilmente anche il rumore del motore. I primi aeroplani di linea a getto degli anni '60 erano famigerati per il loro assordante urlo, mentre i moderni motori turboventola, malgrado incrementino le prestazioni, sono molto meno rumorosi.
A riduzione di questo beneficio c'è il fatto che la resistenza aerodinamica aumenta in maniera esponenziale alle alte velocità, quindi mentre sulla carta il motore turboventola risulta molto più efficiente, nella realtà l'efficienza complessiva è inferiore a quella teorica. Ad esempio, i motori turboventola più recenti (CFM56) del Boeing 737 ad alto rapporto di diluizione lavorano con un'efficienza globale di circa il 30% superiore rispetto ai modelli più vecchi. D'altro canto, i turboventola per aerei militari, specialmente quelli ad alte prestazioni come gli aerei da caccia, possiedono rapporti di diluizione molto bassi tanto da renderli, in alcuni casi limite, affini ai turbogetti (in inglese definiti leaky turbojets[2], in italiano turbogetti a trafilamento).
Raffreddamento della turbina
Il fattore limitante nel progetto di un turbogetto non è il compressore, ma la temperatura sopportabile dalla turbina. È abbastanza facile costruire un motore che possa fornire sufficiente aria compressa che, qualora impiegata per la combustione, possa fondere la turbina; questa era una delle cause principali di rottura dei primi motori tedeschi. I progressi nel raffreddamento ad aria e nei materiali impiegati hanno permesso di aumentare vertiginosamente le temperature di lavoro delle turbine, consentendo un aumento altrettanto marcato dei rapporti di compressione dei motori a getto. I primi motori di prova avevano rapporti forse di 3:1 e i primi motori in produzione come lo Junkers Jumo 004 arrivavano intorno al 4:1, circa quanto i moderni motori a pistoni. I progressi iniziarono immediatamente e non si sono fermati; il più recente Rolls-Royce Trent lavora a circa 40:1, molto oltre qualsiasi motore a pistoni.
Dal momento che il rapporto di compressione è fortemente legato al consumo di combustibile, questo aumento di circa 8 volte nel rapporto di compressione si riflette realmente in un consumo di combustibile di 8 volte inferiore per ogni livello di potenza assegnata al motore. Questa è la ragione per cui l'industria aerospaziale preme tantissimo sull'impiego esclusivo di motori di ultima generazione.
Annotazioni sul progetto
Riepilogo
Prospettiva
Scambio di energia tra il rotore ed il fluido
Il movimento relativo tra le palette ed il fluido ne aumenta la velocità, la pressione o entrambe quando il fluido attraversa il rotore stesso. La velocità viene aumentata dal rotore, mentre lo statore converte l'energia cinetica in energia di pressione. Nei progetti più comuni, nel rotore avviene anche un certo effetto di diffusione.
L'incremento di velocità del fluido dato dal rotore avviene principalmente nella direzione tangenziale e lo statore elimina la quantità di moto in questa direzione (trasformandola appunto in aumento di temperatura e pressione).
L'aumento della pressione si accompagna ad un aumento nella temperatura di ristagno. Assegnata la geometria, l'aumento di temperatura dipende dal quadrato del numero di Mach tangenziale dello stadio del rotore. I motori turboventola attuali hanno ventole che lavorano a Mach 1,7 e più, e richiedono notevoli strutture di contenimento e di abbattimento del rumore per ridurre i danni per perdita della paletta ed il rumore.
Diagrammi di velocità
Gli stadi di palette sono progettati a partire dai diagrammi di velocità. Il diagramma di velocità mostra la velocità relativa tra gli stadi di palette ed il fluido.
Il flusso assiale attraverso il compressore viene mantenuto il più possibile prossimo a Mach 1 per massimizzare la spinta una volta assegnata la taglia del compressore. Il numero di Mach tangenziale determina invece il salto di pressione massimo ottenibile.
Gli stadi di palette fanno ruotare il fluido di un angolo β: angoli più elevati permettono rapporti di temperatura più elevati ma richiedono una robustezza strutturale superiore.
Gli stadi di palette moderni hanno allungamento inferiore e robustezza superiore.
Mappa del compressore
La mappa del compressore ne mostra le prestazioni e permette di determinare le condizioni operative ottimali. Essa mostra in ascissa la portata, in genere come percentuale della portata massica di targa o in unità di misura reali. L'incremento di pressione è indicato in ordinata come rapporto tra la pressione di ristagno all'ingresso ed all'uscita.
Una linea di picco o di stallo identifica il confine a sinistra del quale le prestazioni del compressore si degradano rapidamente e identifica il massimo rapporto di compressione che si può ottenere ad una data portata. Sono riportati anche i limiti di efficienza e le linee di funzionamento per particolari velocità di rotazione.[3]
Stabilità del compressore
L'efficienza del funzionamento è più elevata in prossimità della linea di stallo. Se la pressione a valle dovesse salire oltre il massimo fornibile dal compressore, questo andrebbe in stallo e diventerebbe instabile.
In genere l'instabilità avviene alla frequenza risonanza di Helmholtz (del sistema formato dal compressore e dal volume che si trova appena dopo di esso.
Note
Voci correlate
Altri progetti
Wikiwand - on
Seamless Wikipedia browsing. On steroids.