Cemento (construción)
material de construción coa propiedade de endurecer tras amasalo con auga From Wikipedia, the free encyclopedia
O cemento (derivada do latín cæmentu) é un material cerámico que, en contacto coa auga, produce unha reacción exotérmica de cristalización de produtos hidratados, gañando así resistencia mecánica. É o principal material usado na construción como aglomerante. É unha das principais mercancías mundiais, servindo mesmo como indicador económico dun país.
![]() | Este artigo precisa de máis fontes ou referencias que aparezan nunha publicación acreditada que poidan verificar o seu contido, como libros ou outras publicacións especializadas no tema. Por favor, axude mellorando este artigo. (Desde decembro de 2017.) |
Para outras páxinas con títulos homónimos véxase: Cemento.
Existen diversos tipos de cemento, diferentes pola súa composición, polas súas propiedades e polos seus usos. En xeral, desde un punto de vista químicos, trátanse todos de mesturas de silicatos e aluminatos de calcio.
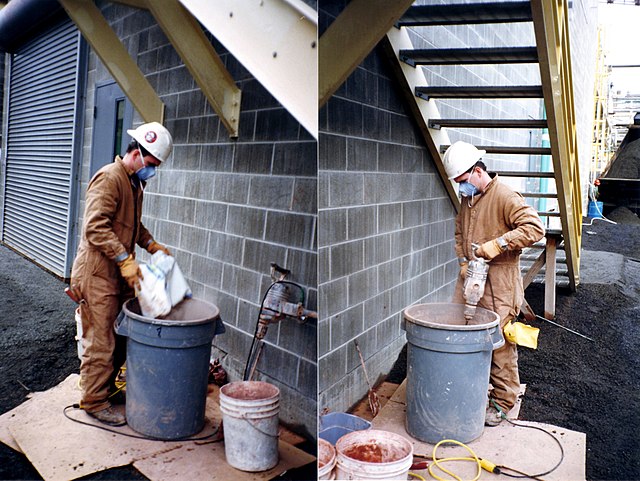
Historia
Xa no Antigo Exipto era utilizada un material feito de xeso calcinado como aglomerante. Entre os gregos e romanos, eran usados solos volcánicos (pozolana) das proximidades de Pozzuoli ou da illa de Santorini, que endurecían despois de mesturados con auga (cementos pozolánicos).
En 1756 o inglés John Smeaton creou unha mestura resistente a través da calcinación de calcarias arxilosas e moles. Ese é o marco da creación do cemento artificial. Tempos despois, en 1824, o construtor, tamén inglés, Joseph Aspdin produciu un po moi fino a partir de pedras calcarias e arxila que, despois de mesturado con auga e seco, producía un material moi ríxido, tanto como as pedras naturalmente empregadas na construción. El bautizou ese material como cemento Portland, en homenaxe á illa de Portland, local onde existían rochas semellantes a ese cemento. Desde entón, ese é o principal tipo de cemento utilizado.
Materias primas
A materia prima máis axeitada para a fabricación do cemento sería aquela que na súa composición química achegase os compoñentes principais do mesmo: cal, sílice, ferro e aluminio. Mais este caso é moi raro que apareza na natureza, polo que ditos compoñentes se obteñen xeralmente da mestura artificial das calcarias e das arxilas.
- As calcarias e as súas variedades conteñen principalmente calcita, e achegan óxido de cal. Tamén achegan aluminio e ferro, combinados en forma de carbonatos e silicatos.
- As rochas arxilosas, compostas na súa maior parte de varios minerais arxilosos, acompañados de numerosas impurezas. Achegan o sílice, alumina e os óxidos de ferro. Tamén compostos prexudiciais como os álcalis (K2, Na2).
- Constituíntes correctores. Cando coas calcarias e as arxilas non é posíbel acadar a composición química desexada para o produción do cemento, é preciso engadir pequenas cantidades doutras materias primas que acheguen as substancias que faltan en cantidades precisas, como pode ser a area cuarzosa, para elevar o contido de sílice; cinzas procedentes do torrado das piritas; ou bauxitas, que aumentan a cantidade de alumina.
Proceso de produción

A produción de cemento Portland segue catro principais procesos: secado, descarbonatación, calcinación e arrefriamento, á parte da preparación previa do cru e a moedura co xeso que se realiza ao final. Tipicamente, a parte central dunha fábrica de cemento, responsábel destes procesos, contén un conxunto de pre-estufa, forno e arrefriador, dispostos nesta orde. Hai aínda procesos de preparación e estocaxe de materias primas, moído de clínquer e limpeza de gases de exhaustión.
Prequecemento
Case a totalidade dos fornos de cemento contan con torres de prequecemento, responsábeis de remover a humidade aínda restante no material tras o proceso de moído alén de iniciar a calcinación do material. Habendo prequecemento, o proceso de produción é chamado proceso de vía seca, máis eficiente e rápido en relación aos procesos de vía húmida, onde a materia prima é alimentada directamente ao forno. Isto débese ás transferencia de calor e masa máis eficientes ocorridas na torre, permitindo se empreguen fornos de lonxitude menor.
Os prequentadores máis usuais son torres de ciclóns. Dispostos en elevadas estruturas (que frecuentemente superan 100 metros de altura), diversos separadores ciclónicos (equipos capaces de retirar partículas sólidas dunha corrente de gases) son interligados entre si. A través da secuencia de ciclóns flúen os gases quentes provenientes do forno, en contracorrente coa materia prima. A medida que esta se mestura co fluxo de gases, ocorre transferencia de calor e transferencia de masa. Nos primeiros momentos do proceso, elimínase a humidade superficial, mentres a temperatura permanece próxima á temperatura de ebulición da auga. A partir deste punto, o material sólido contendo só humidade intergranular pasa a ser quecido gradualmente. No fin do proceso, o material atinxe de 700 °C a 1000 °C, suficiente para a auga sexa eliminada e para se inicien descomposicións químicas da materia prima.
Forno de cemento (forno rotatorio)
A maior parte das reaccións de descarbonatación e formación de silicatos de calcio e aluminatos de calcio ocorren no interior do forno de cemento. Os fornos de cemento son na maioría rotativos, cilindros horizontais de até 160 metros de lonxitude. Un leve ángulo de inclinación combinado ao lento movemento de rotación (de 0,5 a 4,0 rpm) permite que o material percorra o cilindro a medida que desliza polas paredes. Internamente, hai un revestimento de material refractario que protexe a carcasa do forno das altas temperaturas e conservan a calor no seu interior. A materia prima permanece no forno por un tempo de aproximadamente 4 horas e atinxe temperaturas superiores a 1.400 °C suficientes para tornala incandescente e pastosa. A capacidade de produción dun forno medio é 3.000 a 4.000 toneladas por día; os maiores fornos do mundo producen até 10.000.
Arrefriador
Hai dous principais tipos de arrefriadores empregados actualmente. Os fornos máis antigos aínda operativos utilizan arrefriadores satélites, cilindros menores solidarios ao movemento de rotación do forno, encaixados á carcasa do mesmo. Xa os fornos construídos a partir da década de 1980 son dotados xeralmente de arrefriadores de grella, con ventilación forzada, posibilitando maior taxa de transferencia de calor entre o clínquer e o ar entrante. Desta forma, se reduce a temperatura de saída do material, recuperando parte da enerxía asociada ao mesmo, aumentando a eficiencia do sistema.
Alén da eficiencia enerxética, os arrefriadores teñen suma importancia na calidade do produto. O tempo e o perfil de arrefriamento do mesmo son esenciais para a determinación das súas propiedades químicas finais. Lentos procesos de arrefriamento levan á transformación de silicato tricálcico, inestábel á alta temperatura, en silicato bicálcico o que diminúe a resistencia do cemento.
O produto (clínquer) aínda é moído e diluído en xeso, calcaria e/ou escoira siderúrxica para chegar ao produto final.
Combustíbeis
Xeralmente utilízase unha combinación de diversos produtos como aceite, coque de petróleo e residuos industriais. Cerca de 7% das emisións de CO2 no planeta son consecuencia da produción de cemento, debido á combustión e ao proceso de descarbonatación da materia prima.
Aprovéitanse as altas temperaturas e o tempo de permanencia dos gases no forno para empregar combustíbeis de difícil utilización, como pneumáticos picados. Noutras condicións, este tipo de combustíbel podería emitir altas concentracións de substancias extremamente tóxicas (tales como dioxinas e furanos) debido á queima incompleta. Alén diso, a calcaria e a cal contidos na mestura, teñen a característica de reaccionar co xofre proveniente dos combustíbeis, evitando maiores emisións de óxidos de xofre na atmosfera e previndo, por exemplo, a ocorrencia de choiva ácida.
Tipos de cemento
Segundo as normas tecnolóxicas UNE (de España) pódese debullar a seguinte clasificación dos cementos.
Cementos comúns
Existen 27 produtos da familia de cementos comúns, que se agrupan en cinco tipos principais:
- Cemento Portland (CEM I)
- Cemento Portland composto ou mixto (CEM II)
- Cemento de alto forno (CEM III)
- Cemento pozolánico (CEM IV)
- Cemento composto (CEM V)
Cementos con características especiais
- Cementos resistentes aos sulfatos
- Cementos resistentes á auga do mar
- Cementos de baixa calor de hidratación
Cementos brancos
Cementos para usos especiais
Cementos de aluminato de calcio
O cemento de aluminato de calcio foi desenvolvido durante as últimas décadas do século XIX como alternativa ao cementos de silicatos de calcio (cemento Portland), que era obxecto de serios ataques por sulfatos.
Este tipo de cemento tamén ten outros nomes como: cemento aluminoso, cemento de alta alúmina ou cemento fundido de alta alúmina.
Cemento de albanelaría
![]() |
Wikimedia Commons ten máis contidos multimedia na categoría: Cemento ![]() |
Contaminación e efectos perversos
A durabilidade das construcións en cemento son o seu punto forte, pero tamén implica unha debilidade: a superficie cementada anula a súa capacidade de absorción de auga, evitando a drenaxe nas inundacións.
Asemade, a industria cementeira é unha das principais produtoras de dióxido de carbono a nive mundial, estimando a súa porcentaxe de produción en ata un 8 %, e colaborando polo tanto no efecto invernadoiro.
A achega necesaria de area ten esnaquizado zonas de ribeira fluvial ou mariña. Asemade, o gran consumo de auga necesario aumenta o estrés en moitas zonas de gran produción e consumo de cemento que son áridas, semiáridas ou con secas frecuentes.[1]
Notas
Wikiwand - on
Seamless Wikipedia browsing. On steroids.