Ekstrüzyon
Vikipedi'den, özgür ansiklopediden
Ekstrüzyon, enine kesitsel bir profil nesneleri oluşturmak için kullanılan bir süreçtir. Bir malzeme, arzu edilen bir kesitin bir kalıbı boyunca itilir. Basma gerilmeleri ile malzemenin sıkıştırılması ve bir kalıptan o kalıbın şeklini alarak akmaya zorlanması ile gerçekleştirilen şekillendirme işlemidir.[1] Bu sürecin diğer imalat süreçleri üzerindeki iki ana avantajı, çok karmaşık enine kesit oluşturma yeteneği ve basınçlı ve kayma gerilmeleri ile karşılaşan materyallerin kırılgan olmasıdır.
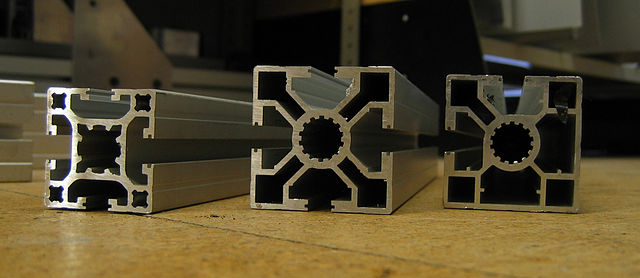
Direkt Ekstrüzyon
Özetle
Bakış açısı

Direkt ekstrüzyonda, konteyner içerisindeki blok, ıstampa tarafından itilerek diğer uçtaki matrisin profil deliğinden geçmesidir. İşlem ileri ekstrüzyon olarak da adlandırılır.[2] İşlem sıcak veya soğuk koşullarda gerçekleştirilebilir. Direkt ekstrüzyonda metal akış yönü ram hareketinin yönü ile aynıdır. Bu proses esnasında blok, konteynerin duvarlarında göreceli olarak kayar. Meydana gelen sürtünme kuvveti de ram basıncının artmasına sağlar.[3] Geleneksel olarak proses 3 ayrı bölümden oluşur:
1. Blok yığıldıktan sonra basınç hızlıca tepe noktasına çıkar.
2. Basınç düşer ve ekstrüzyon kararlı bir şekilde ilerler.
3. Basınç minimuma indikten sonra kısa bir ‘‘atma’’ şeklinde keskin bir şekilde artar[4]
Direkt Ekstrüzyon Yönteminin Avantajları
İstediğimiz boyutlara sahip yarı mamul imalatı sağlar.
Bir çok çeşitte profil kolaylıkla elde edilir.
Takımların sıralanması ve düzenlenmesi kolaydır.
Fabrikada işletme yönünden kolaylık sağlar.
Kalıp tasarımı, konteyner iç çapından bağımsızdır.[5]
Direkt Ekstrüzyon Yönteminin Dezavantajları
Gerekli ekstrüzyon kuvveti yöntemlerden daha yüksektir.
Ekstrüzyon oranı ve hızı istenildiği kadar yükseltilememektedir.
Ekstrüzyon ara iş fazladır.
Malzeme akışı diğer yöntemlerden daha düzensiz olmaktadır.[2]
İndirekt Ekstrüzyon
Endirekt ekstrüzyonda kalıp veya mandrel takoza batar, burada takozun kovana göre bir hareketi söz konusu değildir. Bu nedenle gerekli ekstrüzyon kuvveti azalır.[6]
Ekstrüzyon Şu Üstünlüklere Sahiptir
1. Muhtelif şekillerde yarı-mamullerin üretimi için çok uygundur.
2. Soğuk ekstrüzyonla dayanım arttırmak mümkündür.
3. Ürün boyutlarında yeterli hassasiyeti sağlamak daha kolaydır.
4. Üretim sırasında hurda kaybı daha azdır.[7]
Darbeli Ekstrüzyon
Bu yöntem Pb, Al, Mg, Cu gibi hafif metallerin soğuk olarak kalıpta kullanılmasından elde edilmesidir. İlaç tüpleri bu yolla üretilirler. Bu yöntem indirekt ekstrüzyon ile soğuk ekstrüzyonun birleşik şekli gibidir.[8]
Boru Ekstrüzyon
Bu yöntemle dikişsiz borular üretilir. Silindirik takozlar dolu veya deliklidir. Direkt ekstrüzyonda hem dolu hem delikli takoz kullanılırken indirekt ekstrüzyonda yalnızca delikli takozdan boru üretilir.[9]
Ekstrüzyon Analizi
Ekstrüzyon işleminin analizinde öncelikle deformasyon miktarının belirlenmesi gerekir. Bu amaçla “Ekstrüzyon Oranı” adı verilen parametreden yararlanılır. Bu değer endüstriyel uygulamalarda 16 ile 400 arasında gerçekleşir.
R=Ao÷As
BuradaA0 takozun kesit alanını, As ise ürünün kesi talanını temsil etmektedir. Birim şekil değişimi ε ise;
ε=lnR=lnAo/As
Ekstrüzyon Kalıpları

Ekstrüzyon kalıplarının bazıları açılı olacak şekilde tasarlanmaktadır. Bazılarında ise düz kalıplar (α=90°) kullanılmaktadır. Genellikle alüminyum ve alaşımları için düz kalıplar kullanılırken çelik pirinç gibi malzemelerin ekstrüzyonunda açılı kalıplar tercih edilmektedir. Kalıp açısı seçiminde sürtünmenin ve iç deformasyon işinin dengelendiği optimum değer dikkate alınmaktadır. Optimum açının belirlenmesinde aynı zamanda yağlama ve işlem sıcaklığıda etkin olmaktadır.[12][13]
Ekstrüzyonda Metal Akışı
Ekstrüzyon işleminde alıcı kovanın köşelerinde bir miktar malzeme hareketsiz kalır. Bu bölgeye ölü bölge adı verilir. Ekstrüzyon işleminde ;
a)- En homojen malzeme akışı görülüyor. Metal takoz ile alıcı arasında sürtünme yok. Bu tür malzeme akışı varsa yağlamanın etkisi süper demektir.
b)-Bu tür malzeme akışında sürtünme hayli yüksek demektir. Metal kalıp içine hayli yüksek kayma gerilme değerleri ile girerler. Bu da üründe kusurlara neden olabilir.
c)-Kayma gerilmelerinin hayli yüksek olduğu bir ekstrüzyon işlemi görülmektedir. Demek ki çok yüksek sürtünme var. Bu malzemenin kalıba akışını geciktirmektedir. Metal takozun ortası kolay akarken diğer dış kısımlar zor akar. Sonuçta ölü bölgesi büyük olur. Akma da homojen bir şekilde olmaz. Bu tür bir akış ekstrüzyon kusuru doğurur.[14]
Ekstrüzyon İşleminde Başlıca Kusurlar
1. Merkezde ok başı şeklindeki çatlaklar oluşabilir. Bunun nedeni yetersiz şekil değişimi miktarıdır.
2. Takoz sonuna kadar basıldığı durumda ortadan kolayca ve daha fazla akan malzeme, merkezde ürünün sonuna doğru boru oluşumuna neden olur.
3. Yağlamanın yetersiz olduğu durumda sıcaklığın özellikle yüksek deformasyon hızları nedeniyle arttığı durumlarda yüzey çatlaklarına da rastlanabilir.
Ekstrüzyon işlemlerinde çoğunlukla yatay, hidrolik ekstrüzyon preslerinden yararlanılır. Bu tür presler 500 ile 4000 ton aralığında basma kapasitesine sahiptir. Sıcak ekstrüzyonda takozların ısıtılmasında fırınlardan veya endüksiyon ısıtma donanımından yararlanılmaktadır.[15]
Dış bağlantılar
- eFunda Engineering Fundamentals - Extrusion 19 Ocak 2018 tarihinde Wayback Machine sitesinde arşivlendi.
- 19 Ocak 2018 tarihinde Wayback Machine sitesinde arşivlendi.
Kaynakça
Wikiwand - on
Seamless Wikipedia browsing. On steroids.